Products
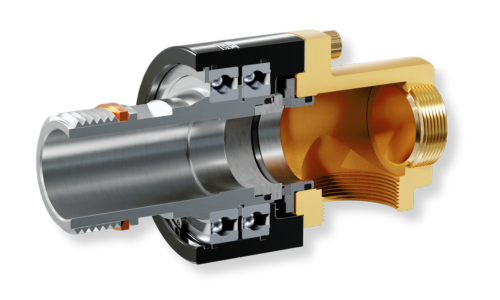
![]() |
![]() |
![]() |
![]() |
- General Purpose Ball Bearing union
- Size from 3/8" up to 8"
- Single and Dual Flow configurations
- Applicable for wide range of fluids
- Exchange of mechanical seal while union is installed on the machine
- Temperature up to 180°C (350°F)
- Max pressure 50 Barg (725 psi)
- Max RPM 3000
MANY CONFIGURATIONS SHIPPING IN 1 DAY
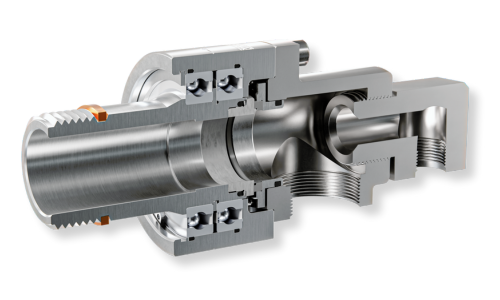
![]() |
![]() |
![]() |
![]() |
- Unions in Stainless Steel AISI 316
- Small union available within 5 working days
- Also Flanged connections possible
- ATEX certification possible
- Optional FDA Seal materials (in contact with fluid)
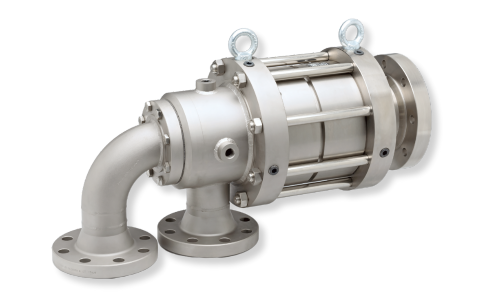
![]() |
![]() |
- Union for High Temperature Oil
- With conical or ball bearings
- External cooling of the lubrication oil
- Available in sizes 1" to 4"
- Temperatures up to 300°C (570°F)
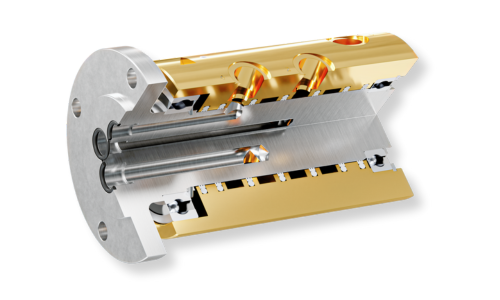
- GM have 2 or more passages
- For tranfering fluids like air and hydraulic oil
- Pressure up to 250 Bar
- Sealing with soft seals or controlled leakage
- central passage for data or electrical cables available

![]() |
![]() |
![]() |
![]() |
- High Speed unions for machine tool applications
- Size from 1/8" up to 1/2"
- Single and Dual Flow configurations
- Applicable for wide range of fluids (Coolant, Air, MQL, Oil)
- Max RPM 50.000
- Max pressure 400 Barg (5800 psi)
- Temperature up to 120°C (250°F)
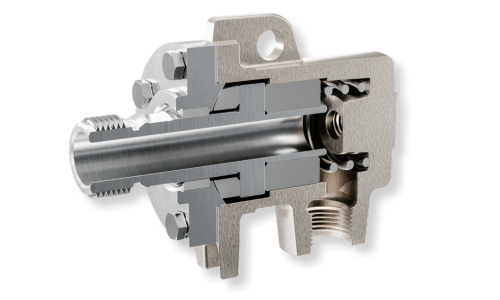
![]() |
![]() |
- Union Designed for Hot Oil
- Size from 3/4" up to 4"
- Single and Dual Flow configurations
- Carbon Guide bearings
- Temperature up to 300°C (570°F)
- Max pressure 35 Barg (500 psi)
- Max RPM 500
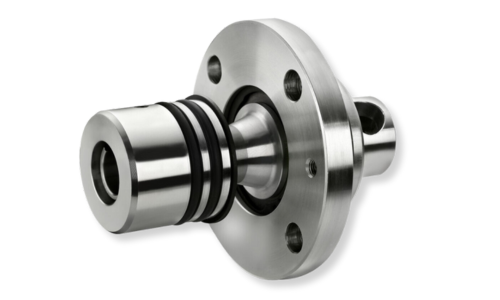
![]() |
- Unions designed specially for the Metal Industry
- Size available: 1/2", 3/4" and 1"
- Single and Dual Flow configurations
- With hard seal faces for abbrasive fluids
- Temperature up to 120°C (250°F)
- Max pressure 10 Barg (145 psi)
- Max RPM 10
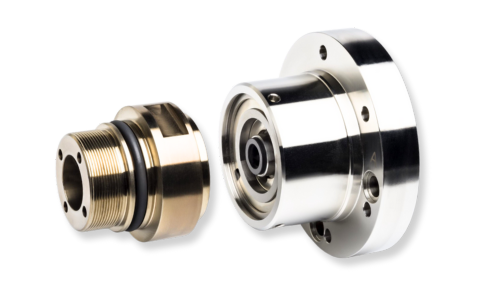
- Johnson-Fluiten can design a union for your application
- We can adapt a existing union or design a new union
- In most cases we test the union before shipping
- Harsh environments, pressures, speeds or fluids?
Send in a request!
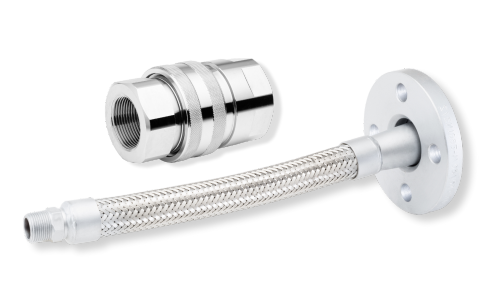
Johnson-Fluiten offers a wide selection of high quality accessories for proper installation of rotary joints on your equipment, as flexible hoses, rotor flanges, couplings and others.
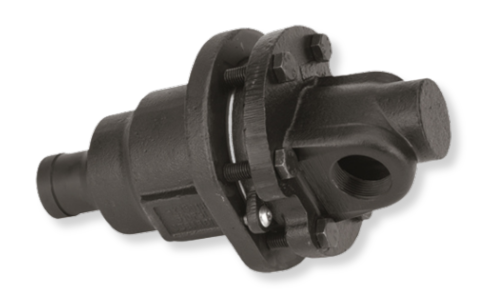
- Designed for oil and steam
- Two internal support guides
- Optimized seal diameter
- Convex seal ring in compression
- Maximum carbon guide separation
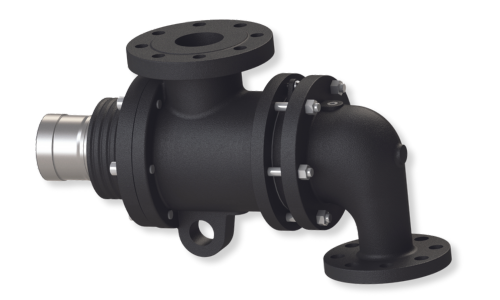
- Robust convex seal design
- Designed for steam and thermal oil
- Wide carbon support guide separation and wear surface
- Standard O-ring or preformed packing
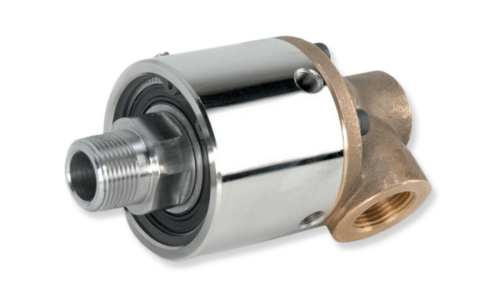
- Balanced seal
- Deep-groove ball bearings
- Full flow area
- External loaded springs
- Matched seal faces
- Integral nipple flange mounting
- On-machine seal replacement
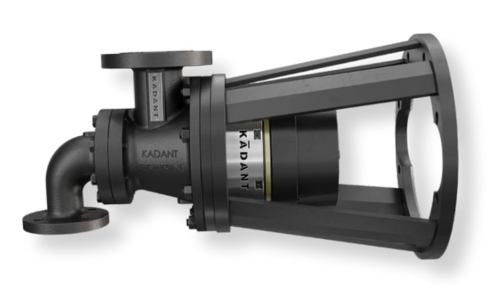
- Proprietary balanced seal design
- 200 psig (14 bar) capability
- Seal cartridge design
- High visibility seal wear indicator
- Protective shroud
- Polished stainless steel end cap
- Large flow passages reduce pressure drops
- Rigid mounting and long end cap
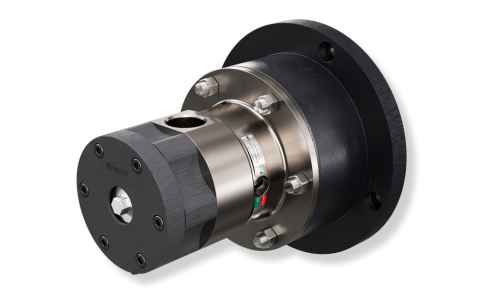
- Balanced seal design with AI technology
- Circular bracket mounting
- Seal wear indicator
- Adjustable syphon clearance
- Operating torque is reduced by nearly 60% compared to conventional steam joints
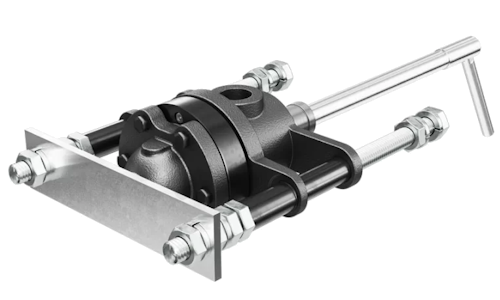
- SecureLock™ syphon retention plate
- Ultra-rigid syphon assembly with self-locking elbow
- Heavy-duty mounting rods with integrated sleeves
- Visual seal ring wear indicator
- Simple upgrade with no piping modifications
WHAT ARE ROTARY JOINTS?
A rotary joint is a sealing device that connects a rotating part to fixed piping for transferring steam, water, diathermic oil, coolant, hydraulic oil, air, and other fluids.
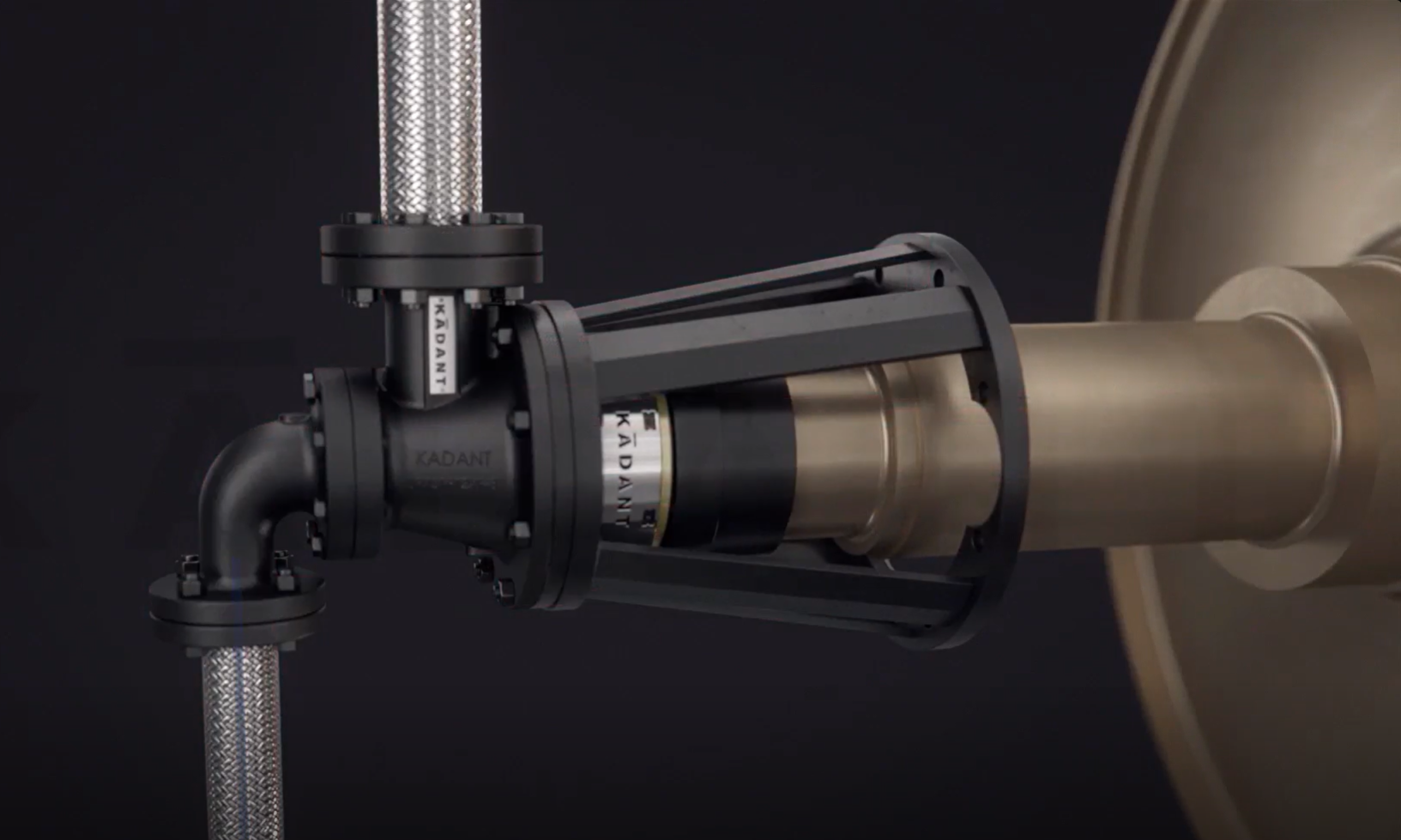
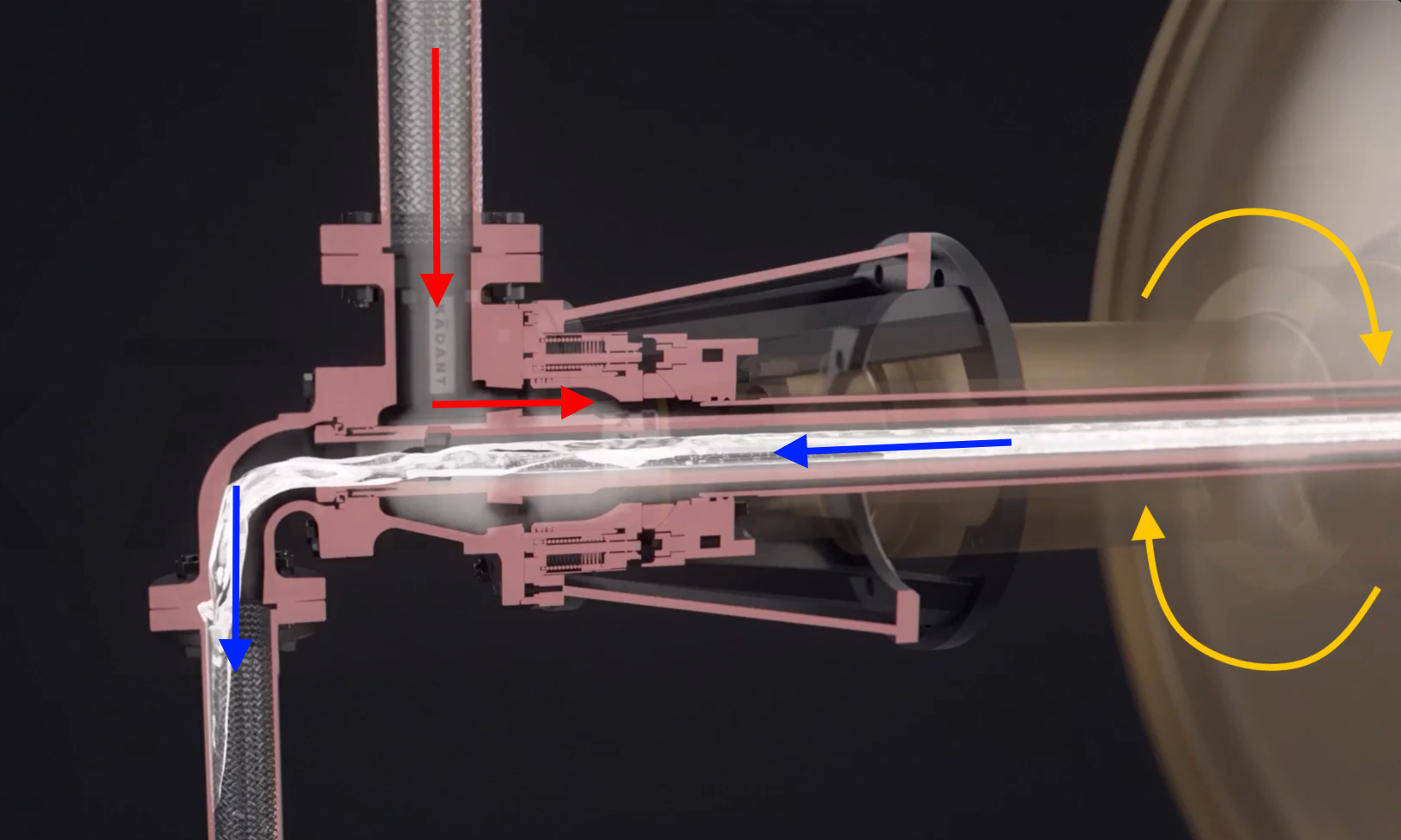
They can be designed with multiple passages and handle multiple types of fluid at the same time. In these cases, a soft seal such as an O-ring is used to prevent fluids from leaking into another passage.
Rotary joints are used in many industries and applications, including oil and gas, food and beverage, aerospace, robotics, and medical devices. In some applications, they are equipped with slip rings to transmit electrical signals and hydraulic power.
Watch our video "what are rotary joints?"
HOW ARE ROTARY JOINTS MADE?
Rotary joints use a spring-loaded seal to prevent fluid, liquid or gas, from being released into the environment. The fluid or gas in many applications is used to create a heat exchange in the product being processed.
For example, steam to dry paper, water to cool the rolls on which metal billets are produced, hot water to heat plastic granules, and cold water to cool plastic film.
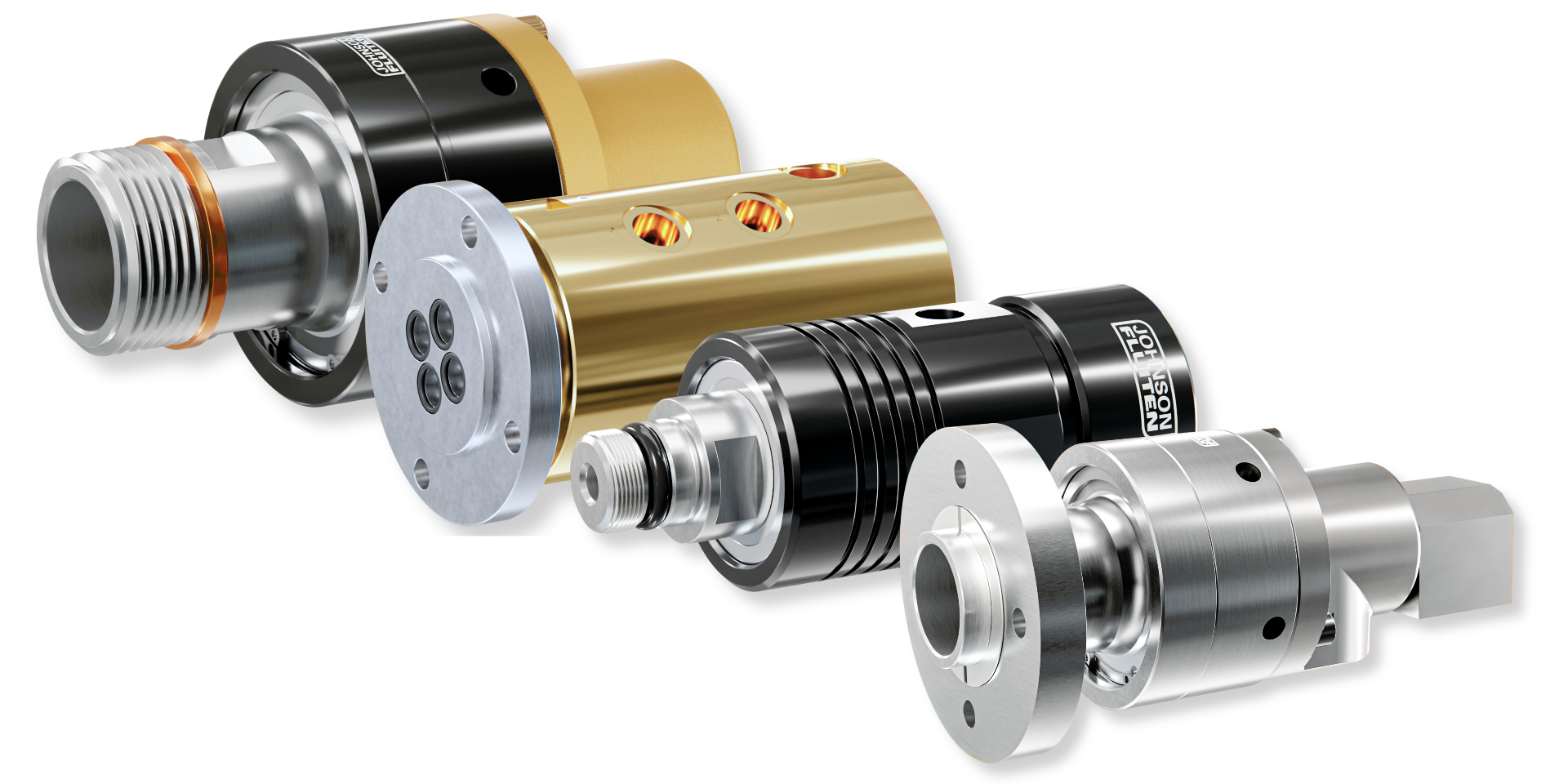
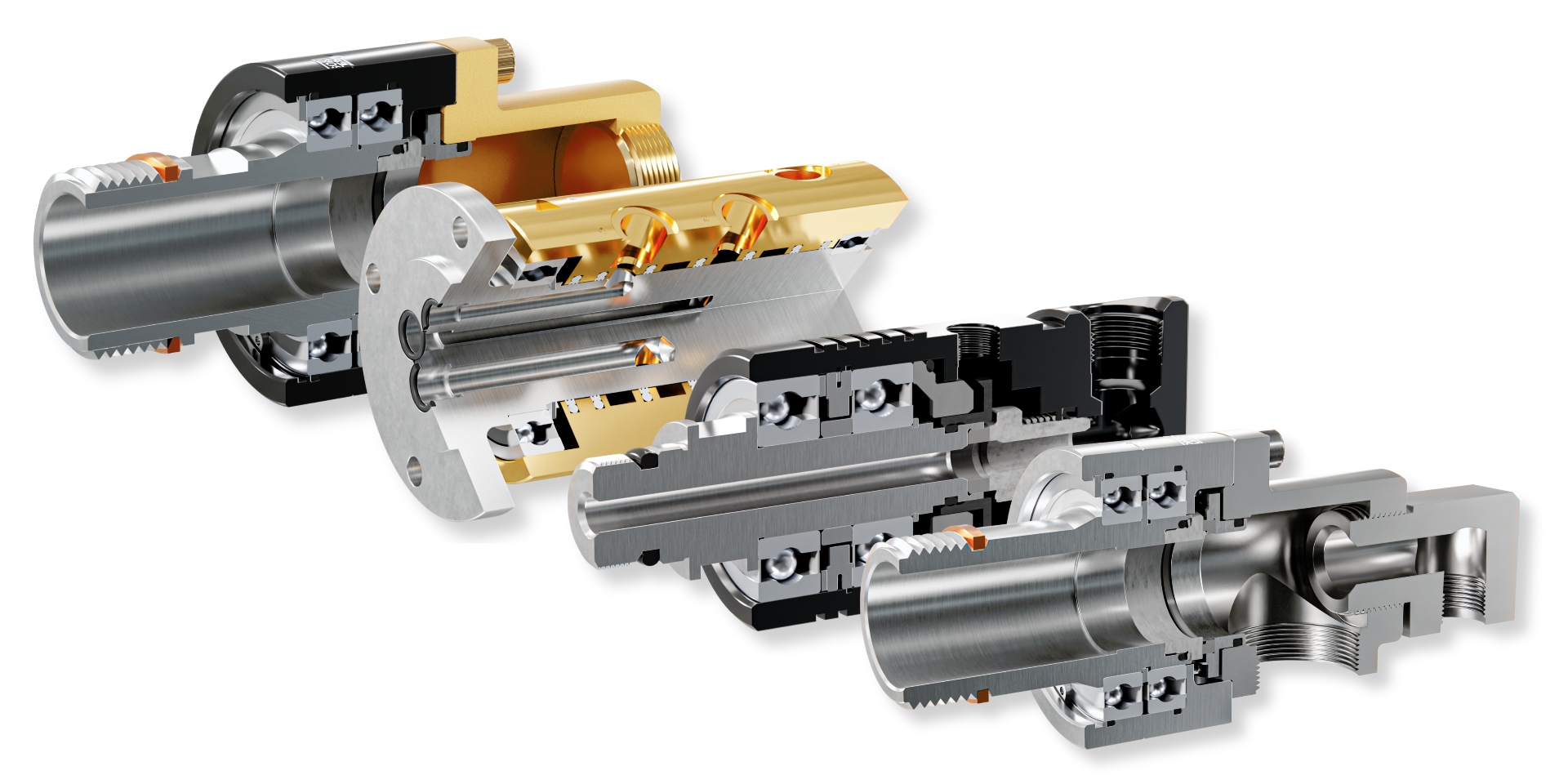
In all these cases, the rotary joint has a mechanical seal, which is the heart of the rotary joint and is either balanced or unbalanced.
With an unbalanced mechanical seal, the spring is used in the rotary joint to maintain the initial internal seat and the rotary joint is pressure sealed once in operation. Low-pressure or vacuum service relies on the spring force to create the seal.
Rotary joints can be self-supporting with the use of an internal graphite rail or externally supported by rods or mounting brackets.
THE BALANCED SEAL
The balanced seal rotary joints are generally used with liquid fluids (e.g., water, coolant, etc.), but they can also be used with steam and other gases.
Balanced sealing technology is based on optimizing spring pressure to create the seal within the rotary joint.
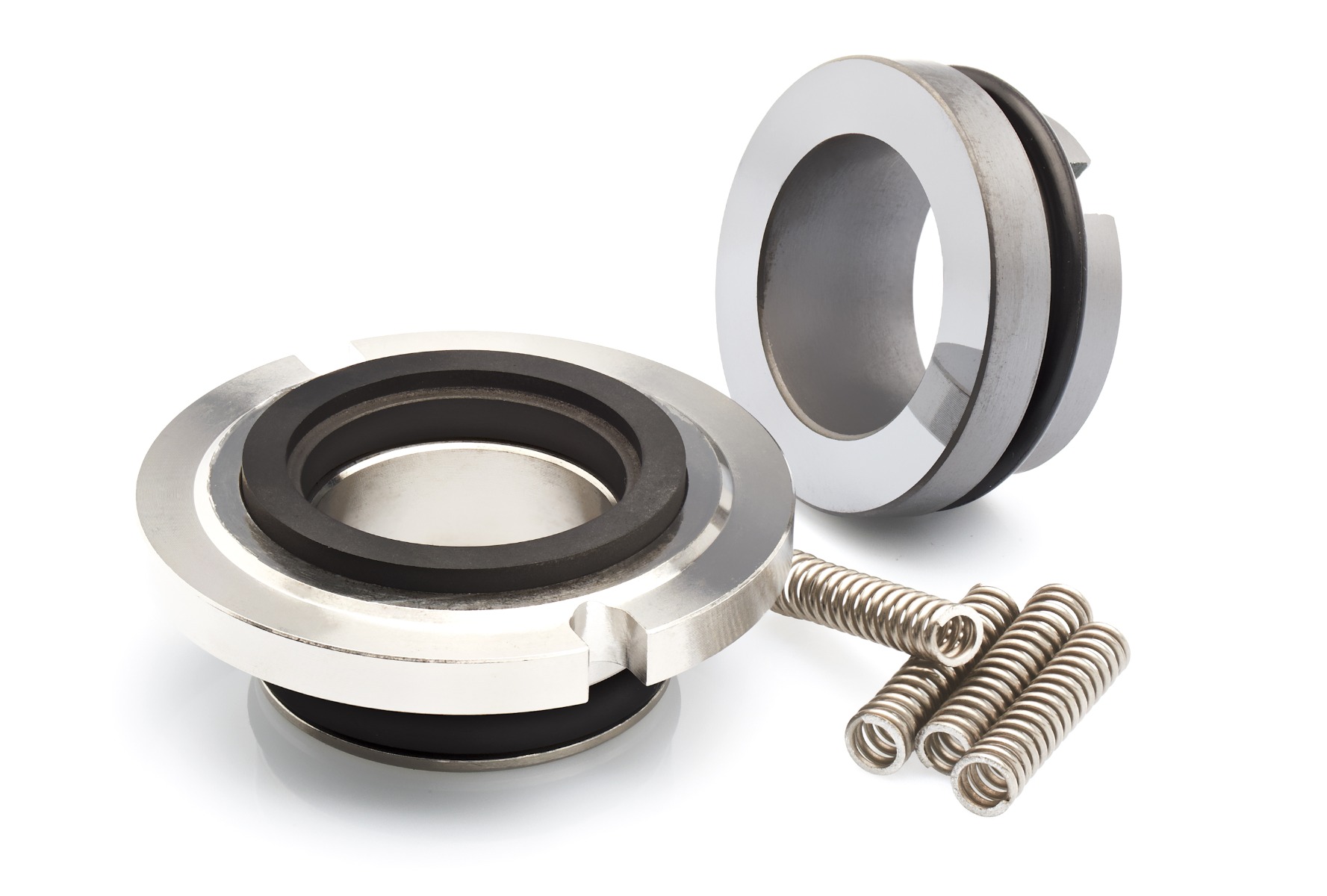
The operating pressure of the fluid has little, if any, effect on the seal load. Balanced seals are typically flat-face seals, and rotary joints are supported by ball bearings.
Seals are the main wear components of a rotary joint and rotating joint. During operation, seals may experience internal loading forces from fluid pressure as well as friction from contact between the seal faces.
Related elements of machine speed, temperature and fluids used can also affect the life of the seal ring. A rotary joint is considered efficient depending on the quality of the seal.
Poor quality seals will wear out faster, resulting in higher maintenance, downtime and repair costs.
When a seal fails, fluid leaks out and the efficiency of the entire heating or cooling process suffers. All this makes the actual cost of replacing the seal only a small part of the total cost of failure.
THE EFFECT OF FLUIDS ON ROTARY JOINTS.
Fluids affect the type of mechanical seal required. Some fluids such as air are not good lubricants. In such cases, two sealing materials are often used, which in combination will create lubrication between the sliding faces.
In other cases, such as water or oil, the fluid will create a very thin lubricating film that will reduce wear on the sealing faces.
Seals are often not made of the same sealing materials: there is usually a harder material and a relatively softer one, which will help the seal faces adapt to each other's wear and tear during their lifetime and remain tightly sealed. Two hard seal materials such as silicon carbide and tungsten carbide can also be used.
Two harder materials are very useful for water that contains dirt particles, such as unfiltered water.
For rotary joint longevity, filtered fluids give the best results.
Do you want to know more?
Here are other essential articles to understand the operation, composition, and selection of these critical components: